MACL has partnered with manufacturer FP McCann to install its first cement-free headwall on a new housing development project in Essex.
The headwall was made using Earth Friendly Concrete (EFC) and was installed at Elsenham Park Housing Development in Essex.
This housing development is being built by Bloor Homes with MACL Ltd the main infrastructure contractor and will consist of 350 new homes when complete.
Chris Wheelwright, MACL’s 278 Works and Infrastructure Manager, said: “We were approached by FP McCann to have the opportunity to trial a cement free headwall early 2024. Knowing how groundbreaking this technology and science is, we wanted to be part of a trial of this nature.
“When we presented the opportunity to our client Bloor Homes along with the adopting water authority, Independent Water Networks Limited, they were also keen to be involved and the Elsenham Park development was the ideal place to do this. The headwall was installed on site on the 12th of September, and we look forward to monitoring its performance and how it integrates with the finished landscaping further down the line.”
FP McCann’s technical team have worked alongside EFC to replace 100% of the cement in the structure with EFC’s binder (comprising activators and supplementary cementitious materials).
The work involved adapting an existing high workability mix design, maintaining the high-quality surface finish while significantly reducing the energy and expense associated with mechanical compaction.
Cement can contribute upwards of 80% of the carbon footprint of plain concrete but another significant contributor in modern construction is steel reinforcement.
For this reason, in addition to introducing EFC binder, FP McCann also replaced traditional steel mesh reinforcement with a synthetic fibre alternative, added during the batching process and evenly distributed throughout the mix.
This combination enables a further reduction in the carbon footprint of the products with an added durability benefit by eliminating the risk of steel corrosion due to aggressive environmental conditions, in turn increasing the service life of the structure. The trials are part of an ongoing initiative at FP McCann to integrate sustainable precast manufacturing solutions, exploring a wide range of options that include use of alternative binders and concrete making materials, increased use of renewable energy sources, optimised structural designs, reducing factory waste and reuse of recycled materials in products.
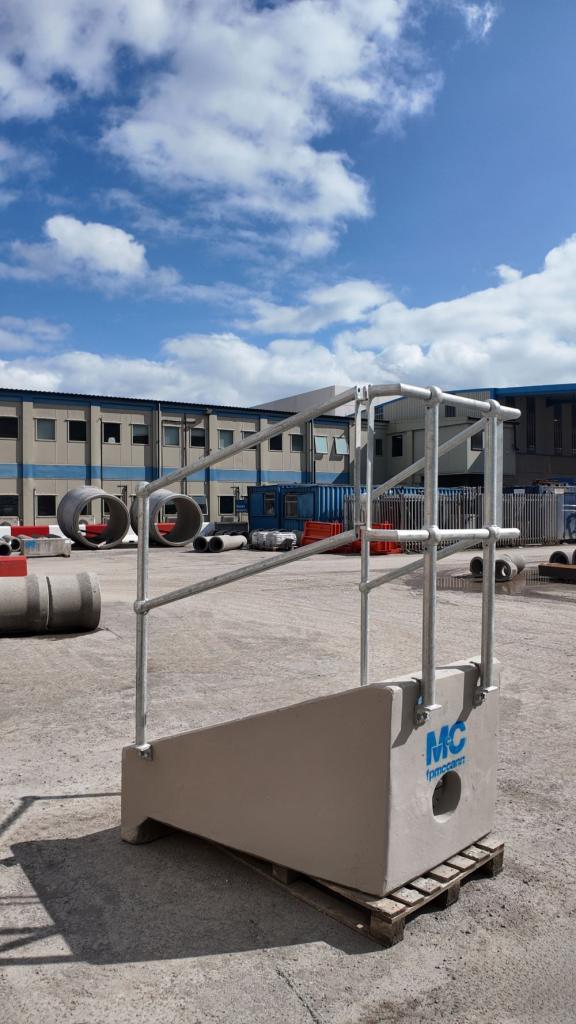
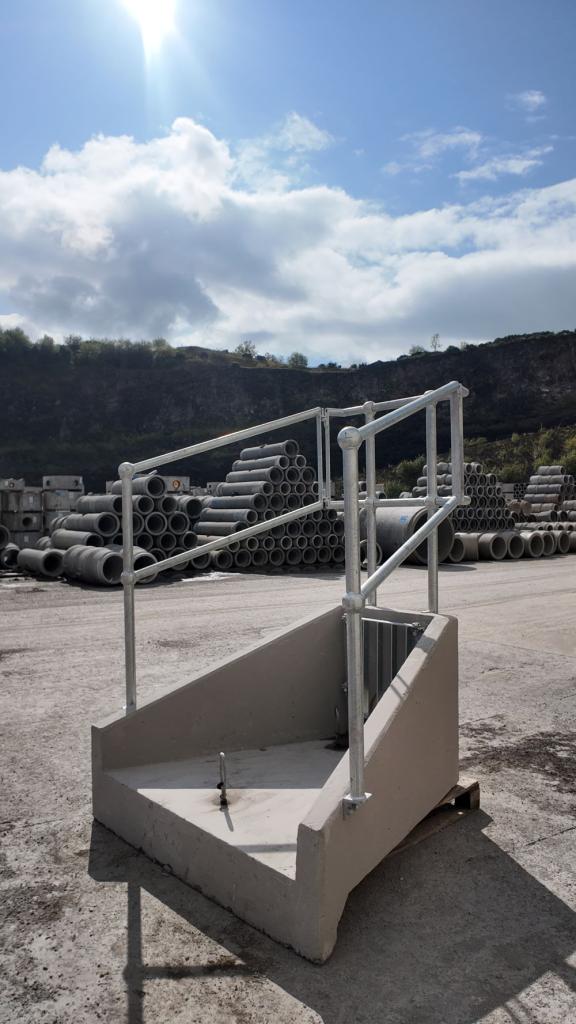